伝説のパソコン:98FELLOW物語(11)ーコストの壁を破るノウハウ
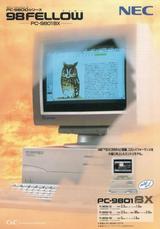
コストの壁を破るノウハウ(2)
コスト低減の王道は「設計のみならず総合的に考えて、早い段階で打てる手を徹底して実行する」ことです。 98FELLOWの開発を通してどのような考え方が役に立ったかをご紹介します。(結果的に後から判ったこともあります)
1.製品コンセプト・仕様を早く明快にする
98FELLOWは「黒船パソコン対抗」&「低価格最優先」&「DOS専用機」(上位の98MATEと棲み分け)の製品コンセプトがクリアで早い段階でFIXしました。
従って、98シリーズの金科玉条だった「過去機種との互換性維持」も98FELLOWの製品コンセプトと照らして、影響が少ない互換性は切り捨てる決断ができコスト低減につながりました。 次のような項目です。
・HDDはファイルスロット形式(SCSI方式)を止め、主流となりつつあり廉価な作りができるIDE方式を採用
・ビジネス用途ではFM音源をあまり使わないため、BEEP音のみとした。
・外部接続の拡張FDDインターフェイスをオプション化
・拡張ボードスロット4スロット→3スロットに削減(98MATEの下位シリーズのため)
しかし、Windowsグラフ・アクセラレータやFM音源ボ-ドなどのアップグレード・パスを提供、CPUは黒船パソコンの上を行く486SX/20を採用するなど、ユーザーに受け入れられる手も打っていました。
また、当然ながら、上位の新シリーズ98MATEとの部品共通化を図り、部品の大量調達により安く調達することも設計条件としました。
2.フロントプロセス・フォーカス
設計や評価のフロントプロセスに集中してリソースを掛けて完全にバグ出しをしてしまうこと、量産移管時点ではお金の掛かる改造・変更は絶対に出さないことです。
これは当たり前のことですが、短納期であり完璧にやることはなかなかに難しいのです。 往々にして潜在問題を残したまま、量産工程に入った後で問題が顕在化し、生産ストップ&特急改造や部品変更による大きな損失が起こり得ます。
特に、パソコンの市場特性から発表・出荷開始日までに、1万台規模の作り溜めをします。
98FELLOWの時は出荷開始日までに5千台の作り溜めが必要でした。
さらに、パソコンのライフサイクルは5ヶ月から6ヶ月で、なおかつ、最初の3ヶ月でライフ総量の80%も占めています。
(図2:パソコンのライフサイクル を参照)
従って、量産移管時点に如何に設計品質が上がっているか、作りやすく生産品質が高くなっているかが、コスト低減に重要なのです。
10万円で売るパソコンに1台当たり数千円も改造や追加部品・変更などの損失費用(オーバヘッド・コスト)が掛かったのでは利益は出せません。
また、量産が近づいた「後ろのプロセス」になると、例えばVCCI(電磁波輻射を抑える規制)対策を打つ場合には、電磁波を抑えるためにコストの掛かる対策部品を何個もシャーシーやマザーボードに取り付けざるを得ない場合があります。
これも、フロント・プロセスで早く評価し対策を織り込めばコストを抑えることができます。 つまり、「臭いものに蓋をする方式ではなく、元を断つ方式」をとる開発コンセプトをメンバーに徹底することが大切です。
3.余裕のある設計をする
前述のように一部互換性を切捨ててて部品を削減し、装置外形寸法は逆に互換性を維持して小さくしなかったため、装置内部の実装スペースに余裕ができました。
これを利用して、マザーボードサイズを広げて全ての回路を入れ込んでしまい、かつ、基板の層数を8層から6層で実現する方針として大幅なコスト低減が図れました。
当時、大きなマザーボードのプリント基板は8層と6層では2~3千円は違いましたし、マザーボード1枚に集約することにより、何枚かのサブボード、ボード間を接続するケーブル、インタフェースのICなどが不要となり、併せて大きなコスト低減となります。
単に、部品コストの低減のみならず、無理して詰め込んだ高密度マザーボードと比べて余裕のある実装密度のFELLOWのマザーボードは組み立て性も良く、SMT歩留まり、検査不良率も少ないという結果となり、生産性・加工費低減の面でも予想以上の効果を発揮しました。
4.余裕のない開発日程でプロジェクト化する
これは逆説的ですが、2ヶ月の超速開発をやった98FELLOWの場合、パソコンの標準開発リードタイム5ヶ月の機種と比べて、総開発費も6割程度、失敗コストもごく少なく、作りやすく生産品質もフィールド品質も良い、従って目標コストをほぼ達成、という結果となりました。
これから言えることは、必ずしも100%当てはまるとは言い切れませんが、熱気をおびた短期集中合同プロジェクト(生産・資材含む)の方が標準的な開発部主導の開発方式よりも良い結果が出やすいということです。
以上まとめると、組織的な「フロント・ローディングのプロジェクト方式」がコスト低減にも大きく寄与するということです。 つまり、製品企画を早くFIXする、開発コンセプトをクリアにする、コスト企画&作りやすさを初期段階で練る、評価バグ出しを前段階で徹底集中する、量産移管前に生産性品質を上げておく、などを組織能力として作り上げることがポイントです。
“伝説のパソコン:98FELLOW物語(11)ーコストの壁を破るノウハウ” に対して1件のコメントがあります。