伝説のパソコン:98FELLOW物語(9)ーBottle-Neck(びんの首)
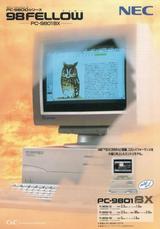
Bottle-Neck(びんの首)
ボトルネック(Bottle-Neck)を辞書で引くと[びんの首、狭い通路、仕事の進行などで障害となるもの、隘路]とあります。
また、IT情報用語辞典では、「生産工程の中にはボトルネックとなる工程があり、それが全体のスループット(生産量)を決定する。
最適生産のためには工程全体のスケジュールをボトルネック工程の能力に合わせる必要があり、生産性向上のためにはボトルネック工程を重点的に改善すべきだ」という生産管理・改善の制約理論(TOC)のキーワードとなっています。
開発のプロセスでもボトルネック工程があり、他の設計プロセスと並行できず期間が長いため、全体の開発リードタイムの最短長を決定してしまう要素があります。
パソコン開発の場合のボトルネック工程の大物は、
①マザーボードのプリント基板(回路配線基板)
と
②PCケースの構造板金とフロントマスクなどモールドの金型の設計製造リードタイムです。
①のマザーボードは、設計に1ヶ月、製造に2W、②の金型は1次TRY品が1.5ヶ月、そこから修正を織り込んだ2次Try品を経て、最終金型の3次品まで1ヶ月、合わせて2.5ヶ月が標準的なリードタイムでした。
これでは、98FELLOWの目標開発期間:2ヵ月には全く当てはめることはできません。
このボトルネック設計工程も何としてでも短縮させるしかありません。
編み出した手は次のようなものでした。
1.マザーボードのリードタイム半減
マザーボードのような大型プリント基板は多層(8層や6層)構成です。配線設計(パターン設計と言う)に時間が掛かっていたのは、CPUやメモリ周辺の高密度でパターンを密集して通さねばならない部分です。
当時、自動配線CADも使い始めていましたが、この高密度部分はCADではお手上げで、人間の知恵でパターンを引くしかありませんでした。(業界で名の通ったパターン設計請負の天才肌の職人が何人かいたものです)
<採った施策>
・天才肌の職人に難しい高密度部分に集中させ、24時間2シフト設計を行う。
・パターン設計請負先を2社使い、競争させて早くできたものを使う。
・オーバーラップ:回路図はできたものから順次パターン設計にリリース。
・マザーボード寸法は大きく取り部品実装密度を下げる:パターン配線をし易くする。
・出来上がったパターン図は大人数で分割チェックし1日で終わらせる(通常は1W)
・評価を早く始めるために短納期基板を別枠で発注(当時出回りだした3~4日で製造できる短納期基板、少量限定で価格は高い)
→このような手を打ち、通常6W掛かっていたマザーボードのプリント基板の設計・製造を3Wで実現しました。
2.構造板金、モールド金型のリードタイム半減
大量生産するためには、金型が必須です。大量に作るために2つ以上の金型を作る場合もあります。 金型設計・製造で時間がかかる要因を調べてみると
①リリースした図面の解釈や図面だけでは分からない調整事項などのやりとりや変更・修正指示に時間が掛かっている
②金型メーカーでもリスクマージンを取った金型リードタイムを設定している、他に何点も金型注文を受けて掛け持ちしている
③1stTRY→2ndTry→FinalTryと修正・改善を繰り返すステップが当たり前となっており時間が掛かっている、などが判りました。
<採った施策>
・実績と技術力のある金型メーカーを選び98FELLOWプロジェクトへの専任協力体制を依頼
・早く図面出しするために、前の機種の図面流用&修正で2Wで作成する
(PC98の互換性維持ポリシー:前機種と外形寸法は変えないことが役にたった)
・2ndTryとFinalTRYを合体させ、リードタイム短縮を図ることを初めから宣言
・当方の構造設計のメンバーを金型メーカーへある期間常駐し調整検討を一気にやってしまう。金型メーカーの進捗管理や金型1stTry品の立ち上げにも参加する。
・ボード、エレキ系の評価を先行スタートするために、ベースフレーム板金シャーシを金型品とは別にNC加工で特急に作り、オーバーラップさせた。
・フロントローディングの徹底;構造設計のデザインレビューを構造グループに加えてボード、装置、生産技術のメンバーと集中的に実施して初期段階に図面へ反映。
→通常1.5ヵ月掛かっていた、金型の1stTry品の入手を3.5Wに短縮することができました。 併せて、通常2.5ヶ月掛かっていたFinalTRY品までの時間も結果的に6.5Wで達成することになります。
Thanks in favor of sharing such a pleasant opinion,
article is pleasant, thats why i have read it fully